Water Soluble Supports - PART ONE
Many hobbyists and engineers are familiar with single extruder 3D printing, but dual extrusion and soluble supports printing is less common. Soluble supports, whether water soluble, or alkaline soluble (eg. Stratasys SR-30), enable complex geometry to be printed without the need for sacrificing overhang surface quality or manual labor involved in support removal.
COMPLEX GEOMETRY
SOLUBLE supports allow you to dissolve supports in complex geometries. THis is especially useful for models where it would be difficult to remove supports by hand. It also reduces labor significantly when printing large volumes of parts that require support removal.
Aside from soluble supports allowing you to have better surface finish and labor reduction, they also enable the following:
Printing without a part cooling fan
Printing at higher extrusion temperature
Both of the points above lead to greater inter-layer adhesion and overall part strength, minimizing the anisotropic nature of FDM/FFF as much as possible. If one were to try this with a single extruder, surface finish during bridging would be compromised and/or your part would fuse to your support structure.
A popular 3D printing youtuber shows some tests on PLA/PETG as a function of cooling temperature (https://www.youtube.com/watch?v=Bl2ESvtBiLo). Printing at higher extrusion temperatures can also increase the layer adhesion strength.
PART STRENGTH
Taken from the CNC Kitchen youtube video linked above - this compares tensile strength tests with varying levels of cooling vs tensile strength in the xy direction which is the strongest in FDM/FFF.
Water soluble supports such as PVA or BVOH are typically reserved for use with filaments like PLA or Nylon. It’s uncommon to use these materials with amorphous polymers like ABS or PC due to low adhesion to each other. There are a wide array of other water soluble supports that claim “high temperature” and “excellent adhesion” to amorphous polymers, but there is little proof or test data of these claims across the board.
At Ember, we’ve spent a significant amount of time getting BVOH to work with amorphous polymers. Although BVOH does not have tremendous adhesion strength to these polymers, there are tricks involved in maximizing adhesion and getting good results (eg. printing really hot, having high flow multipliers at interfaces, and having larger extrusion widths on support interfaces). There are some occasions where a specific filament type and geometry result in a very challenging part with BVOH. These are typically scenarios where a large, dense part is attached to a BVOH surface without a heated chamber. Since adhesion strength is not that high, the part will typically warp away in these scenarios. These instances require further tricks to maximize success, or use of a different support material altogether.
In another blog post, we’ll cover how we’ve begun testing other soluble support materials such as the 3DXTech X1 Universal Support Material, which is made in the USA, and has great adhesion results with amorphous polymers as well as Nylon and Glass-filled Nylon. We’ve thrown many different part geometries at this across all the materials we own and it really prints and adheres well to all parts. We’ll also be comparing some other brands and taking a deeper dive into soluble supports. The goal is to converge on a support material that is easy to print with, has better adherence than BVOH to a wide range of materials, and has good solubility. Stay tuned for our follow up post!

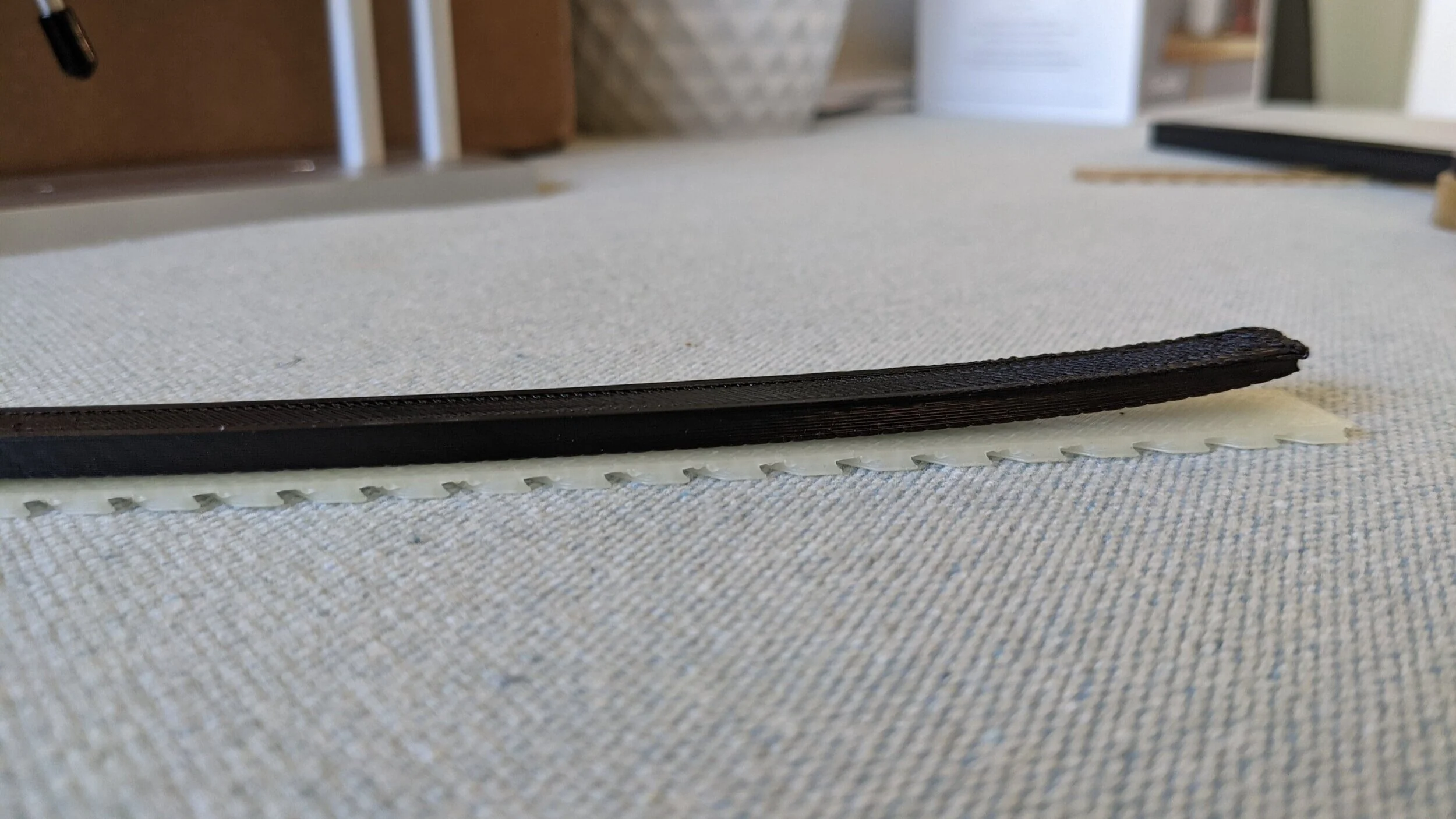
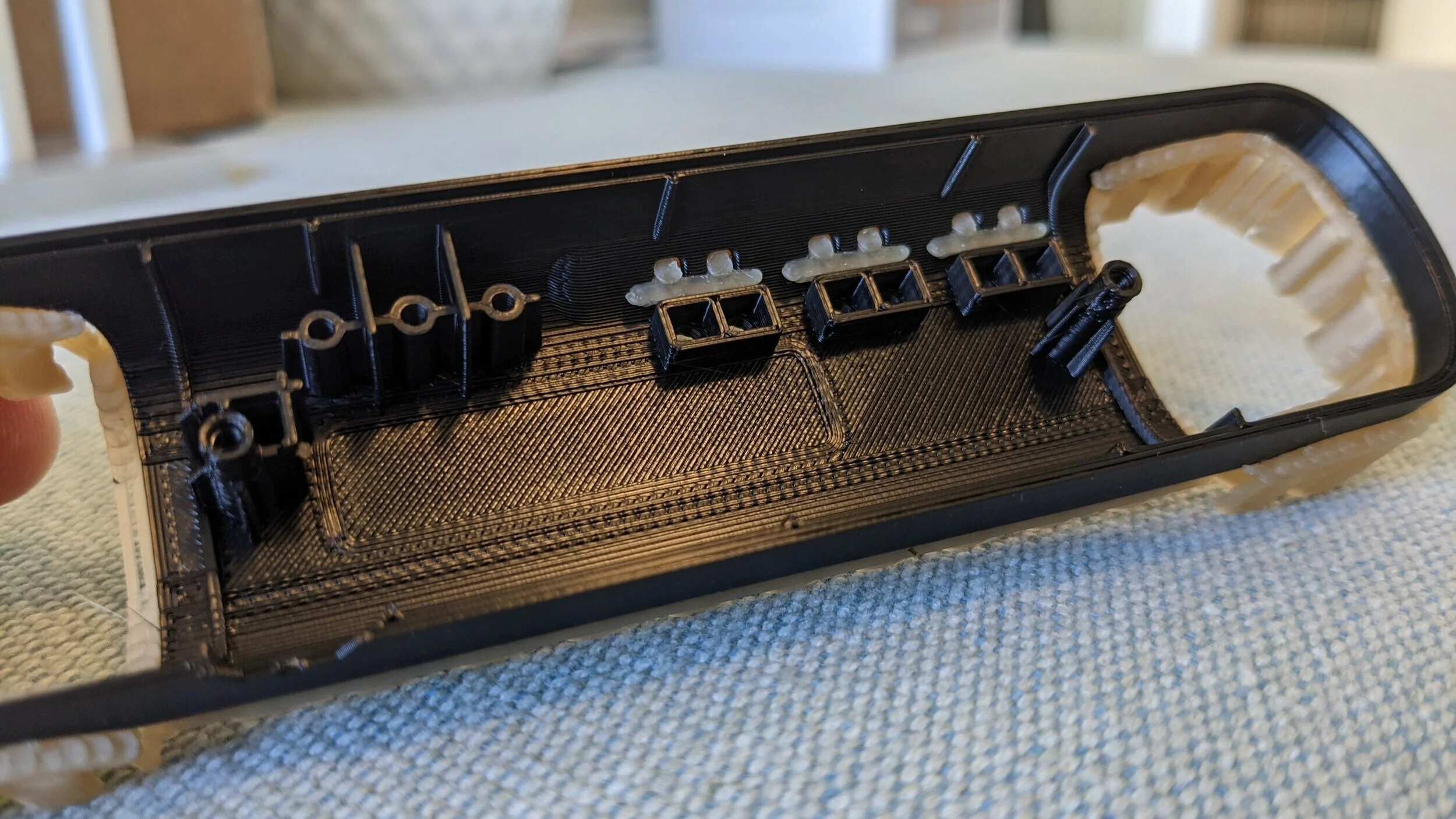
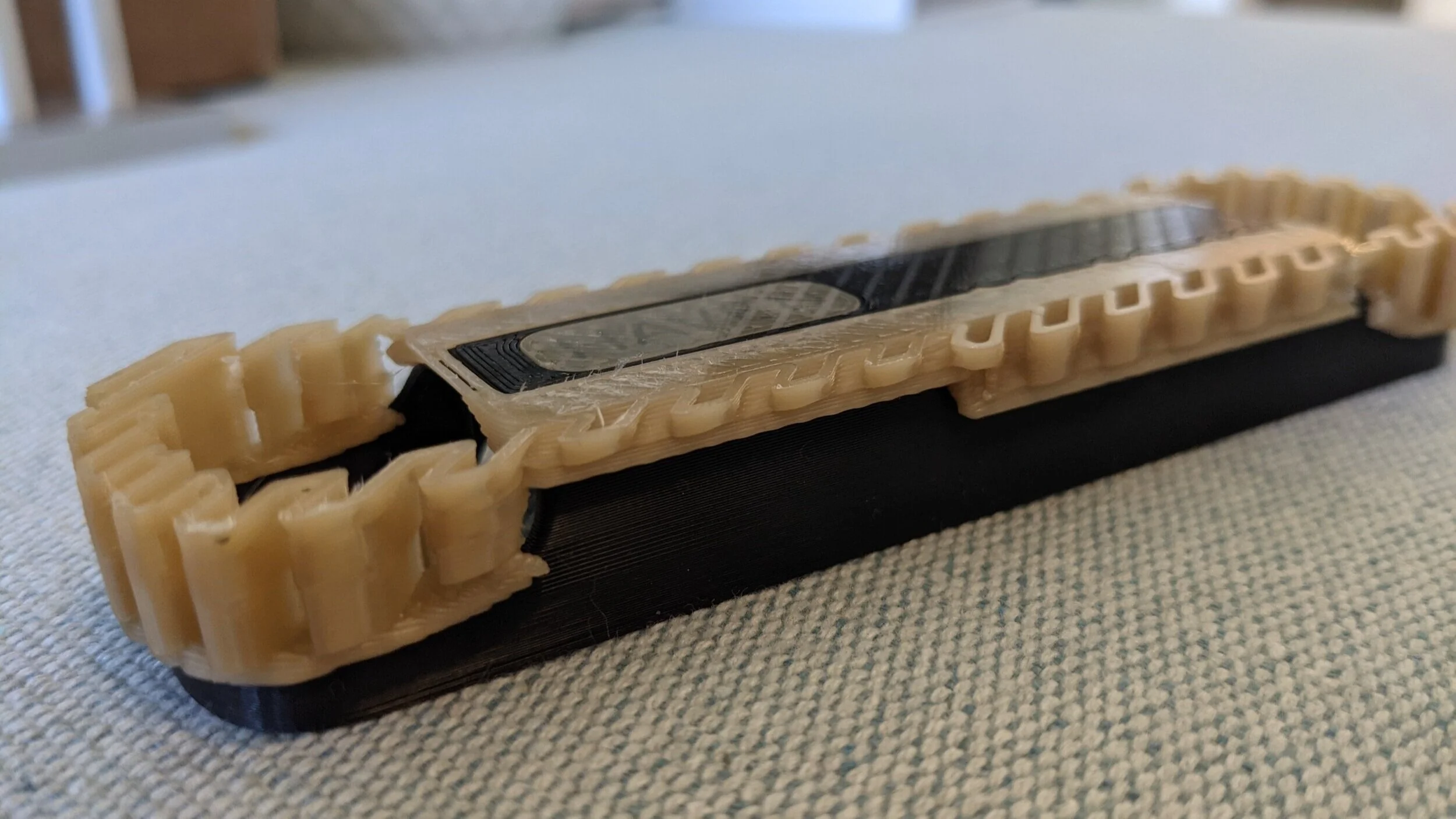

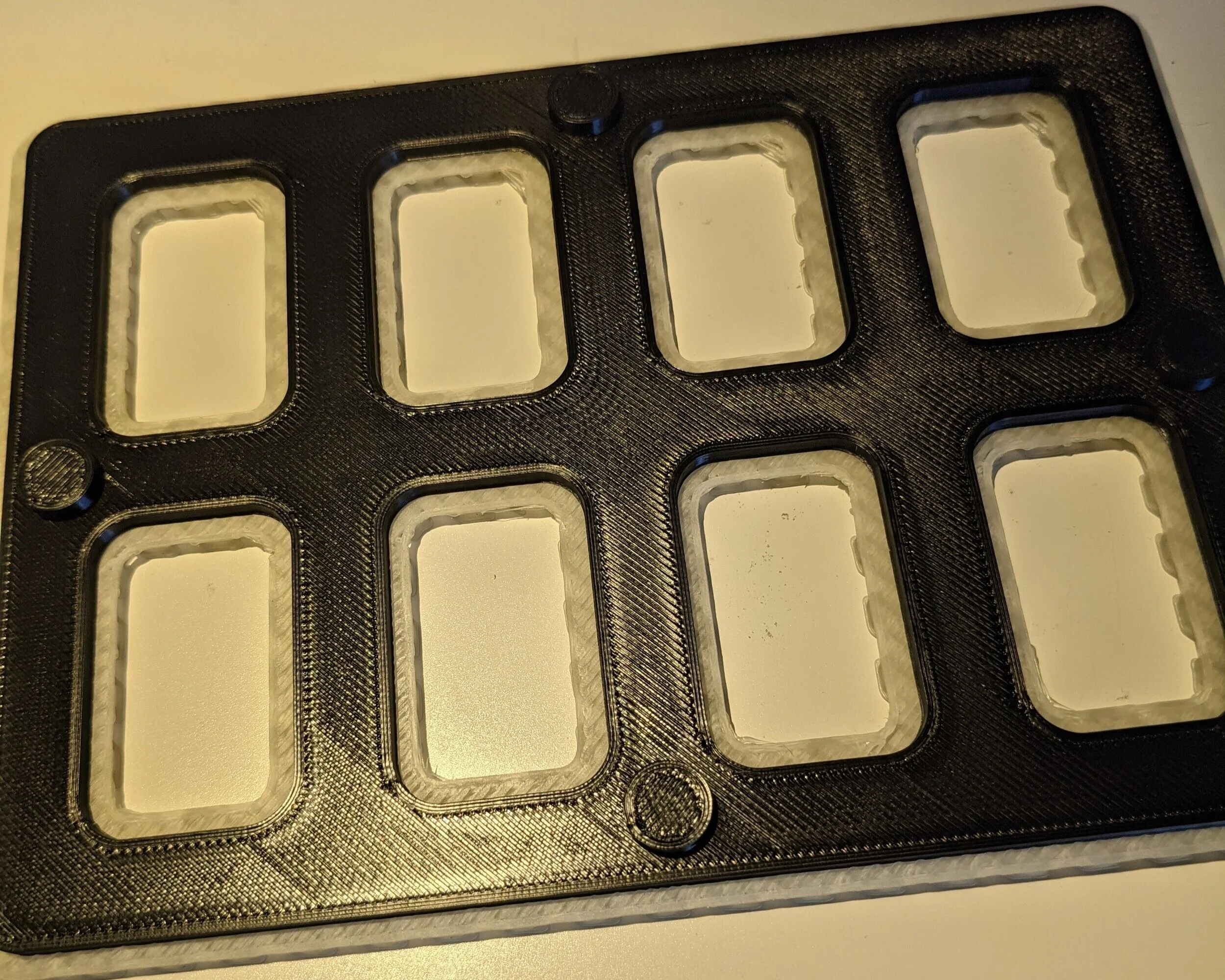
